EASA Part 145 is Annex II to IR Maintenance and details the standards with which an organisation must comply in order to be approved to carry out maintenance of aircraft. Any aircraft used for commercial air transport must be maintained in accordance with the terms of Part 145.
EASA Part 145 approval is granted by an organisation known as the ’competent authority’. If the maintenance organisation is situated inside the EU then the competent authority is national aviation authority of that country . If the organisation is outside the EU then the competent authority is EASA itself. The procedures which the competent authority must follow are laid down in Section B of Part 145. Section B of Part 145 will not be discussed on this Article.
Let us list down the sections of EASA part 145 Regulation. please click the link for the full text.
SECTION A — TECHNICAL REQUIREMENTS
145.A.10 Scope
145.A.15 Application
145.A.20 Terms of Approval
145.A.25 Facility requirements
145.A.30 Personnel requirements
145.A.35 Certifying staff and support staff
145.A.36 Records of airworthiness review staff
145.A.40 Equipment and tools
145.A.42 Components
145.A.45 Maintenance data
145.A.47 Production planning
145.A.48 Performance of maintenance
145.A.50 Certification of maintenance
145.A.55 Maintenance and airworthiness review records
145.A.60 Occurrence reporting
145.A.65 Safety and quality policy, maintenance procedures and quality system
145.A.70 Maintenance organisation exposition
145.A.75 Privileges of the organisation
145.A.80 Limitations on the organisation
145.A.90 Continued validity
145.A.95 Findings
SECTION B — PROCEDURE FOR COMPETENT AUTHORITIES
145.B.01 Scope
145.B.10 Competent authority
145.B.15 Organisations located in several Member States
145.B.20 Initial approval
145.B.25 Issue of approval
145.B.30 Continuation of an approval
145.B.35 Changes
145.B.40 Changes to the Maintenance Organisation Exposition
145.B.45 Revocation, suspension and limitation of approval
145.B.50 Findings
145.B.55 Record-keeping
145.B.60 Exemptions
We have briefly explained EASA part 145 by sub sections in our own words below.
In order to gain approval the organisation produces a document known as an exposition. Exposition details how the requirements of Part 145 will be met. The format of this Maintenance Organisation Exposition (MOE) is detailed in Part 145.
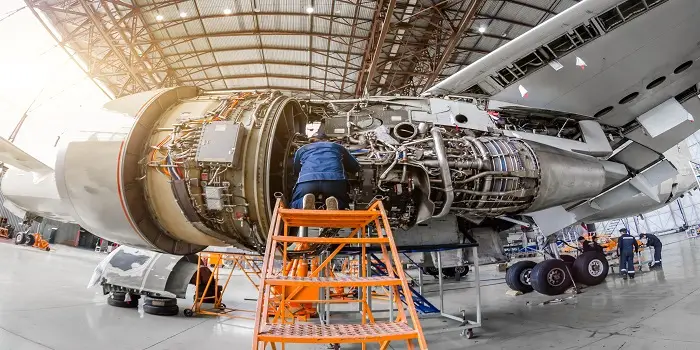
Facility Requirements (Part 145.A.25)
- The organisation must demonstrate that there are sufficient, suitable facilities for the work which they intend to carry out. This applies not only to the hangars for maintenance. It also to workshops for component overhaul and office accommodation for management and administration functions.
- Working areas must be enough lighting and temperature control to allow staff to carry out activities safely. Also, there should be a minimum of noise to reduce the risk of mistakes due to distraction. Hangars must be protected to ensure that the work area is not contaminated by rain, snow or dust. There must also be sufficient space for the aircraft and any necessary support equipment required for maintenance.
- Workshop space must be provided for all planned overhaul work on components.
- Where appropriate it must be shown that there is separation between different areas such as clean and dirty rooms for composite repair or separate workshops for different types of battery.
- Storage facilities for aircraft components must be provided and they must be secure. Entry is restricted to authorised personnel only. Additionally, there must be segregation between storage areas used for serviceable,
- repairable and unrepairable components. The storage areas must contain enough racking for storage. These areas sufficient temperature control and ventilation to prevent excessive condensation.
- Office areas must be provided to accommodate all management and administrative activities. This can be all in one place as long as there is enough space for all activities to take place. Certifying staff must have space to study maintenance data required and to update the aircraft paperwork as work progresses.
Personnel Requirements (Part 145.A.30)
- The organization must appoint an ’accountable manager’ who has overall responsibility to ensure resources available to carry out the work.. The accountable manager must be acceptable to the competent authority but need not necessarily have technical knowledge. It also is the accountable manager’s responsibility to promote the company’s safety and quality policy.
- The company must also appoint a person responsible for the compliance of EASA Part 145 requirements all times. These persons must be acceptable to the authority. The company must declare their responsibilities and their deputies incase of their absence.
- The accountable manager has to appoint a quality manager who is responsible for setting up quality system. Quality System must be and independent from main operation and maintained at all times,
- The organisation must also demonstrate that it has a man hour plan. This manhour plan must show that all activities can be adequately staffed for all planned activities. The manhour plan has to take into account all activities of the company. these activities must include work on non EU aircraft as well as non-Part 145 work. The manpower should consist of no more than 50% sub contract staff, the rest should be employed by the company directly. Where the staff are sub contracted, they must nevertheless always work in accordance with the company’s procedures. The manhour plan includes not only the production staff but also quality, planning and all other functions. The manhour plan must be reviewed at least every three months and updated when necessary.
- The organisation must establish and control the competence of all maintenance, management and quality audit staff to ensure that an acceptable level of competence is maintained. This would include their technical competence as well as their knowledge of human factors. In order to fulfil this function the organisation must put into place a procedure for assessing the employees’ competence and must keep records of all the qualification and competence assessments. A basic job description should be created for each position to assist in the assessment of competence. Further guidance can be found in AMC 145.A.30(e). Human factors initial training should also be tailored to the particular job function as different functions will encounter different human factors issues. Human factors refresher training (referred to as continuation.
- The organisation must demonstrate that it has sufficient qualified staff to carry out non destructive testing (NDT) on aircraft. The only NDT method that can be carried out by B1 staff is the colour contrast dye penetrant test.
- If an organisation wishes to run a line station then it must have enough B1 and B2 certifying staff. This means that they must have enough staff who are B1 and B2 licence holders and who have undergone a qualification process allowing them to release aircraft back into service after maintenance has been carried out. Additionally, the organisation may employ Cat A line certifying mechanics to support the B1/B2 staff. This means that the line station could run with less B1/B2s but not without them completely.
- If the organisation wishes to carry out base maintenance activities it must have sufficient Cat C certifying staff as well as B1/B2 staff working as support staff. In this situation the B1/B2 support staff supervise each individual task and then, when all tasks have been completed, the Cat C base certifying engineer makes the final certification to release the aircraft back to service.
- EASA Part 145 states that component certifying staff shall comply with Part 66. A check of Part 66 reveals that at the present time there are no licences for component certifying staff and that they should continue to be certified in accordance with the applicable national standards. In the UK this is covered by British Civil Airworthiness Requirements (BCARs).
- There are certain cases in which maintenance can be carried out by non licence holders, these mostly concern activities outside the EU or when the aircraft is away from base. If an organisation is based outside the EU but gains EASA Part 145 approval it would be very difficult and expensive to only be able to employ Part 66 licence holders as certifying and support staff. Provision is made for them to use holders of licences issued in that country instead. Another exception is where an aircraft is stuck at a remote location and there is no EASA Part 145 organisation there who can repair it. In this case a local licensed engineer with the relevant experience and training could be given a one off authorisation to carry out the job. In some cases a repetitive preflight airworthiness directive can be carried out by the flight crew and not necessarily by a Part 66 licence holder.In both of the above cases the EASA Part 145 organisation must establish the competence of the person to carry out the work and must keep a record of all details.
145.A.35 Certifying Staff
The organisation must ensure that the certifying staff and support staff have adequate understanding of the aircraft or equipment to be maintained and of the relevant company procedures. This must be done before the authorization is issued and the organisation has a responsibility to keep records of all information supporting the authorisation.
In order to be awarded certifying staff or support staff privileges the applicant must:
- hold a Part 66 licence in the relevant category.
- hold a type rating for that aircraft.
- be able to demonstrate sufficient recent experience.
- be over 21 years of age.
When the above criteria have been met the organisation must assess the individual’s competence and knowledge of the relevant company procedures.
This is carried out by the quality department of the company.
When all of these conditions have been met the organisation will issue the certification authorisation document to the individual. This document will clearly specify the extent and limitations of the holder’s privileges. The period of validity of the authorisation is normally no longer than the period of validity of the Part 66 licence.
In order to retain the authorisation the individual must be able to demonstrate that he has maintained each of the conditions of initial issue detailed above.
This means that;
- the licence must be renewed and not allowed to run out of date,
- the holder must carry out sufficient work on that aircraft type to maintain recency,
- the holder must undergo sufficient continuation training every two years.
Continuation training is training carried out within the company to ensure that all certifying and support staff are kept up to date as much as possible with changes to the aircraft, the company procedures relevant to their job, national and international regulations, and any other requirements relevant to them. Additionally, the training must include some human factors training. If this training is not carried out or the engineer does not carry out sufficient work on that aircraft type or the licence becomes out of date the authorization becomes invalid.
It is the responsibility of the organisation to keep all records which support the authorisations, this would include;
- details of Part 66 licence held.
- all relevant training completed.
- the scope of the authorisation issued.
- details of staff with limited or one-off authorisation.
Records of all authorisations and supporting documentation must be held by the organisation for at least two years after the person leaves the organization or the authorisation is withdrawn.
The issue and control of the staff authorisations and the record keeping is the responsibility of the quality department.
If requested, the organisation must give the holder of the authorisation a copy of it when he leaves the company.
145.A.40 Equipment, Tools and Material
The EASA Part 145 organisation must have available and use the correct equipment and tools to carry out all of the work for which it is authorised.
If a manufacturer says that a particular tool must be used to do a certain job then this tool must be used unless permission is gained to use an alternative.
All of this tooling must be available all of the time that work is to be carried out.
this includes nights and weekends if applicable. It is not necessarily required that the tools be owned by that organisation, just that they are available whenever required. If an agreement is in place with another organisation to loan tools when required then this should be acceptable.
A base maintenance organisation must also show that they have sufficient access equipment (ladders, steps, safety raisers etc.) to carry out the work safely and effectively.
Any tools used to carry out measurements, settings or tests on the aircraft must have a calibration and inspection program in place in accordance with the manufacturer’s instructions. This includes, amongst other things, torque wrenches, precision measuring equipment, test sets, crimping tools and electrical meters. The company must keep a record of all of these tools including their inspection and calibration status and records of any repairs.
145.A.42 Acceptance of Components
- All components within the company must be classified and segregated into one of the following categories;
Serviceable and accompanied by the appropriate paperwork. Appropriate paperwork refers to the release certificate which accompanies the component. This paperwork will be explained in detail later.
Unserviceable components which shall be maintained by a EASA Part 145 organisation.
Unsalvageable components which cannot be repaired or maintained. These components must be prevented from re-entering the supply chain. Eventually these parts will be destroyed or stored until such a time that a repair scheme is created.
Standard parts. These are parts which are manufactured to a recognized standard for use on aircraft and are specified in the aircraft’s parts catalogue.
Materials which meet the required specification and traceability. This includes all raw and consumable materials used in the maintenance activity.
- The organisation is responsible for ensuring that all components fitted are eligible to be fitted on the particular aircraft or piece of equipment. This must take into account any modifications or airworthiness directives. Eligibility
information is included on the release certificate and may contain vital airworthiness information required by the user.
The organisation must be satisfied that the component is in satisfactory condition and has the necessary release paperwork. It must also be ascertained that the component is the correct one and meets the approved standard. This is done by comparison with the manufacturer’s manuals or with other approved information such as service bulletins etc.
- The EASA Part 145 organisation may gain approval to fabricate certain components for its own use. These components are limited in their scope and cannot be used outside the organisation or supplied to another organisation. Examples of components which may be fabricated can be found in AMC 145.A.42(c).
145.A.45 Maintenance Data
Maintenance data refers to all data required to carry out all of the work for which the company is authorised.
Maintenance data would typically include;
- all relevant manufacturers’ documentation such as AMM, IPC, SRM etc,
- airworthiness directives and service bulletins applicable to the aircraft or equipment maintained by the organisation,
- repair drawings, drawing standards, NDT manuals,
- standard practices information such as CAAIPs,
- applicable national and international requirements such as EASA Part 145, BCARs, etc.
The organisation must show that all of this data is available to the people who need it at all times when work is being carried out.
Additionally, the organisation must put into place a system for ensuring that the maintenance data is always kept up to date and a register should be available so that the engineer can check that the data in use is the most up to date version.
There must also be a system in place to allow any inaccuracies or ambiguities in a publication to be reported to the author. This would consist of an internal system which employees could use to report such inaccuracies. The information would then be gathered together at one point in the company, usually quality, and then transmitted to the relevant organisations outside the company.
Also part of maintenance data is the workcard system. This is the system which creates all the individual jobcards for all of the maintenance activities which the company carries out. All of the relevant technical data for that task must appear on the job card so it is clear to the reader exactly what actions are required. This can either be the printing of detailed instructions on the jobcard or, more likely, a reference to the relevant maintenance data. This takes the form;
’Carry out lubrication of left hand main landing gear IAW AMM Ch……’
If the task is long or complicated the card entry must have several stages so it is clear to the reader exactly what is required and so that the individual tasks can be signed off as the job progresses. The cards should have separate entries for disassembly and reassembly.
Provision should also be made for when a third-party aircraft is to be maintained and it is required to use the third party organisation’s paperwork system.
In this case it is acceptable to use the third party’s system but a procedure must be in place to ensure that the paperwork is used correctly.
145.A.47 Production Planning
A system must be put in place to plan the availability of personnel, tools, equipment, material, maintenance data and facilities to ensure that all work can be carried out safely. This could range from a very simple system to an extremely complex arrangement involving a dedicated department depending on the size and complexity of the organisation.
The planning system should ensure that any scheduled work does not interfere in any way with other work with regards to personnel, facilities, etc. and should provide organisation of shifts in order that there is no undue time pressure.
This has to take into account human factors issues such as length of shifts, night shifts etc.
The final element in production planning is that there should be an effective system of handover of information from one shift to another. If a job is to be continued by a new team of personnel during the next shift period it is essential that all information is handed from the outgoing shift to the oncoming shift with no room for omission or error. Firstly it must be stated that all work carried out must be recorded and signed for at the end of each shift and not allowed to build up and all be signed at the end of the job (some jobs can be weeks long).
This is carried out on the aircraft paperwork which is kept as part of the aircraft’s maintenance record. This information, however is not always sufficient to give a comprehensive handover at shift change so an additional system is required. The system normally takes the form of a diary in which relevant handover information is written. This information must be clear and unambiguous in order that the oncoming shift can interpret it and carry on with the task with no chance of work being missed out or duplicated.
145.A.50 Certification of Maintenance
A Certificate of Release to Service (CRS) must be issued after every maintenance action before the aircraft can be flown. In the case of component maintenance, the CRS must be issued before the component is released to be installed on the aircraft. This certification can only be made by appropriately authorised certifying staff on behalf of the EASA Part 145 organisation (already mentioned in 145.A.35). CRSs may only be issued for tasks within the scope of the
organisation’s approval, this scope is detailed in the exposition.
Depending on the organisation’s capabilities, CRSs may be issued for work on various types of aircraft, overhaul or maintenance of certain types of components or the carrying out of certain repair techniques. An organisation may
have approval to certify one or a combination of these activities.
The CRS has a prescribed wording;
’Certifies that the work specified except as otherwise specified was carried out in accordance with Part-145 and in respect to that work the aircraft/aircraft component is considered ready for release to service’.
- In the case of work on the aircraft the certification is made in the technical log of that aircraft.
- In the case of a base maintenance check the certification is made on a worksheet which closes the check, this certification is then entered into the aircraft tech log.
- In the case of a component the certification is made on the Authorised Release Certificate (EASA Form 1).
Depending on the company procedure, the certifying staff member will either sign the CRS, stamp it with a unique stamp issued to him at the time of approval or sign it and stamp it.
It is also permissible to use a computer based workcard system in which the CRS would be made by entering a PIN code unique to, and known only by, the certifying staff member.
The method in use will be detailed in the company procedures.
It has been stated that every component must have a valid EASA Form 1 before it can be fitted to an aircraft. There is one exception to this rule. If an aircraft is grounded at a remote location away from it’s main base or any line station
and there is no suitably certified component available, it is permissible to temporarily fit a component with no EASA Form 1. The component must have some form of certification (for example from a non EU country) and must otherwise be serviceable and satisfy all other operational and legal requirements.
This component must be removed or appropriate certification obtained within 30 flight hours or on return to the main line station or main base.
145.A.55 Maintenance Records
Records must be kept of all details of maintenance carried out by the organisation. These records must be kept for at least two years from the date that the aircraft or piece of equipment was released to service. The purpose of this is to
provide a reliable and accurate record of all maintenance activities on a certain aircraft or piece of equipment. As far as possible the records should be stored in such a way to protect them from fire, flood or theft and the records must be of a good enough quality to be still legible and useful after the period of storage.
If some records are lost for any reason eg. fire or flood, the records can be reconstructed as far as possible by reference to other documentation such as mechanics’ own records and overhaul documentation from other organisations. In this case the reconstructed records would have to be submitted to the NAA for inspection. If there are still gaps in the records then additional aircraft work may be required to ensure that the aircraft is in an airworthy condition.
It is acceptable to have a computer based records system provided that an adequate level of security can be shown and that a backup is made within 24 hours of any maintenance activity.
145.A.60 Occurrence Reporting
It is the responsibility of the organisation to report any condition of the aircraft or component which has resulted or could result in an unsafe condition which hazards flight safety. The report must be made to the NAA, the aircraft
operator and the aircraft design organisation.
Examples of conditions which would be reportable are; burning to components or structure, deformation of the structure, failure during test of essential equipment.
The object of this system is to identify the factors contributing to aircraft incidents, and to make the system resistant to similar errors.
In order to do this the organisation must set up an occurrence reporting scheme which can be used by the engineers to report any unsafe conditions. This information will then be collated together, normally by the quality department, and then forwarded, in the agreed format, to the relevant parties. This system should also include a monitoring function to identify any adverse trends which may be uncovered.
The report should include the following information;
- Organisation name and approval reference,
- Information identifying the aircraft or component,
- Date, time and information on aircraft or component life (hours, cycles etc.),
- Details of the identified unsafe condition,
- Any other relevant information found during evaluation or rectification of the condition.
The report must reach the authority as soon as possible but, in any case, no later than 72 hours from the time the condition is discovered.
In order for such a system to function it is essential that the company create a culture in which the reporting of unsafe conditions and the cooperation with investigations is in no way punished. This will encourage open and honest reporting and help to prevent a culture of covering up problems.
The system should be a closed loop so that the progress and findings of the investigation are fed back to the individuals involved in reporting it.
145.A.65 Safety and Quality Policy, Maintenance Procedures and Quality System
The organisation must establish a safety and quality policy which must be included in the Maintenance Organisation Exposition MOE. The safety and quality policy must include a statement committing the organisation to;
- Recognise safety as a prime consideration at all times,
- Apply human factors principles,
- Encourage personnel to report maintenance related errors and incidents,
- Recognise that compliance with procedures, quality standards, safety standards and regulations is the duty of all personnel,
- Recognise the need for all personnel to cooperate with the quality system.
The organisation must put into place procedures covering all maintenance activities to take into account human factors and human performance issues and to ensure good maintenance practices.
Especially important is ’error capture’ in safety critical systems. This means that the procedures would guard against one tradesman from making the same error on multiple systems and causing a flight safety incident. An example is engine oil replenishment, the procedures should ensure as far as possible that one tradesman could not leave all the oil filler caps off and cause severe oil loss from all engines.
The organisation must establish a quality system which must audit the organisation. The purpose of this system is to ensure that the organization maintains a safe standard of work at all times and remains in compliance with the standards laid down by EASA Part 145.
An essential part of this system is the independent audit, all areas of the company must be audited in every twelve-month period. This audit is independent in that it is carried out by personnel who are not responsible for the activity being audited. For example, if a battery servicing facility is to be audited then the audit must be carried out by personnel who do not carry out the battery servicing. In larger organisations there will be a staff of dedicated auditors who are responsible to the quality manager. The quality manager has ultimate responsibility for the operation of the quality system.
The quality system must include a feedback system which ensures that the findings of the audits are communicated to the relevant persons within the company so that the necessary corrective actions can be carried out.
All audit records must be held for at least two years from the date of closure of the audit.
145.A.70 Maintenance Organisation Exposition
This document, often referred to as the MOE is a book which explains how the organisation is going to comply with EASA Part 145. It will contain all the information required by the national authority to issue or re-issue the EASA Part 145 approval.
The book is an approved document and any changes to it must be approved by the authority.
The MOE will comprise eight parts;
Part 1 Management
This part will detail the structure of the company, the names and titles of all of the nominated staff and will contain a statement of corporate commitment by the accountable manager. Also in this part will be the company’s scope of work and procedures detailing how the amendments to the MOE will be incorporated.
Part 2 Maintenance Procedures
This part details the procedures which must be followed when carrying out any maintenance activities. It will include procedures for the acceptance and calibration of tools and equipment, modification procedures, planning procedures, shift handover procedures and other procedures governing every area of aircraft and component maintenance.
Part 3 Quality System Procedures
This part contains the procedures used by to maintain the quality system. It will detail how audits will be carried out, how they will recorded and how the findings will be followed up. Additionally, the human factors training procedure and the competence assessment of personnel will be included.
Part 4
This part will contain a list of contracted operators. These are organisations whose aircraft maintenance is routinely carried out by the EASA Part 145 company and for which an approved contract exists.
Part 5
This part will list contractors, sub-contractors and line stations.
Part 6 Operators Maintenance Procedures
Where an organisation is an operator and holds EASA Part 145 then this section will comprise procedures used inside the company.
Part 7/8 Supplementry Procedures for FAR 145 Repair Stations and Transport Canada Civil Aviation Maintenance Organisations, respectively
These parts are used when an organisation is approved under USA or Canadian regulations as well as EASA regulations. Their purpose is to highlight the difference between the sets of regulations.
145.A.75 Privileges of the Organisation
Privileges of the organisation refers to what the organisation is allowed to do under its approval. The first thing listed is that the organisation may carry out maintenance of the aircraft or components for which it has approval at the locations described in the exposition. This means it can carry out planned maintenance only at the listed locations. The organisation may, however carry out unplanned maintenance at any location if the aircraft goes unserviceable there.
For example, if an aircraft is grounded at a location not listed in the MOE because of a fault, the organisation could rectify the fault at that location but not carry out a scheduled maintenance there. Additionally, the organisation may sub-contract work to another organisation to carry out. There are restrictions on this sub-contracting, only certain types of work can be sub contracted (normally specialist services such as welding or plating) and the organisation carrying out the work must be fully covered by the EASA Part 145 organisation’s quality system as the work will be certified under the Part 145 approval.
For example, if a EASA Part 145 organisation has a component which needs to be metal plated as part of a maintenance activity but does not have the capability to do the work itself, it may have this work done by a specialist company. The Part 145 organisation can then certify this work under its own approval. In order to ensure the quality of work and the adequacy of the specialist company’s procedures, the company must be overseen by the quality system of the Part 145 organisation. This oversight will be detailed in the MOE.
For all of the above activities the Part 145 organisation may issue certificates of release to service and allow the aircraft to fly or the component to be fitted to the aircraft.
145.A.80 Limitations on the Organisation
The organisation may only carry out the work for which it is approved when all of the necessary tools, facilities, personnel etc are available.
This paragraph allows for a situation when an organisation does not have sufficient tools, equipment etc but it is only a temporary situation. During this time the NAA would suspend the organisation’s approval to do that particular type of work until the tools, equipment etc are available again. There is no need for the approval certificate to be re-issued or for the approval schedule to be changed.
145.A.85 Changes to the Organisation
The organisation gains its approval on the basis of the company MOE, thus if there was any change to the company, the MOE would become invalid and the organisation would be non-compliant. Any proposed change to the organization such as change of facilities, change of staff, change of name etc should therefore be notified to the NAA as soon as possible so the changes can be discussed and approved before they come into effect. The MOE is then amended to reflect the changes. This way the approval can carry on uninterrupted with the minimum effect on the company’s operation.
The process for notifying changes to the NAA and for amending the MOE will be detailed in the MOE.
145.A.90 Continued Validity
When the approval is issued it has no expiry date and its validity is open ended. On two condition
1.the company remains in compliance with Part 145
2.that the competent authority is granted access to carry out its audits.
The NAA must audit the company every year and for this they must be granted reasonable access to the organisation. The organisation must ensure that the NAA has access to any sub-contracted company working under the organisation’s approval. (Sub-contracting is described above in 145.A.75).
145.A.95 Findings
When the NAA carries out its audits it will compare the standards found in the organisation with the standards laid down in the regulations. If there are any areas where the organisation is not in compliance then this is called a finding
and will be highlighted to the organisation at the end of the audit.
Obviously some of these findings will be more serious than others so there are two classifications;
- A level 1 findings – is any significant non-compliance with Part 145 requirements which lowers the safety standard and hazards seriously the flight safety.
- A level 2 finding – is any non-compliance with the Part 145 requirements which could lower the safety standard and possibly hazard the flight safety.
When these findings have been notified to the organisation, then the responsible persons in the company must define the corrective actions to be taken. He must also carry out the corrective actions to the satisfaction of the authority.
Read more